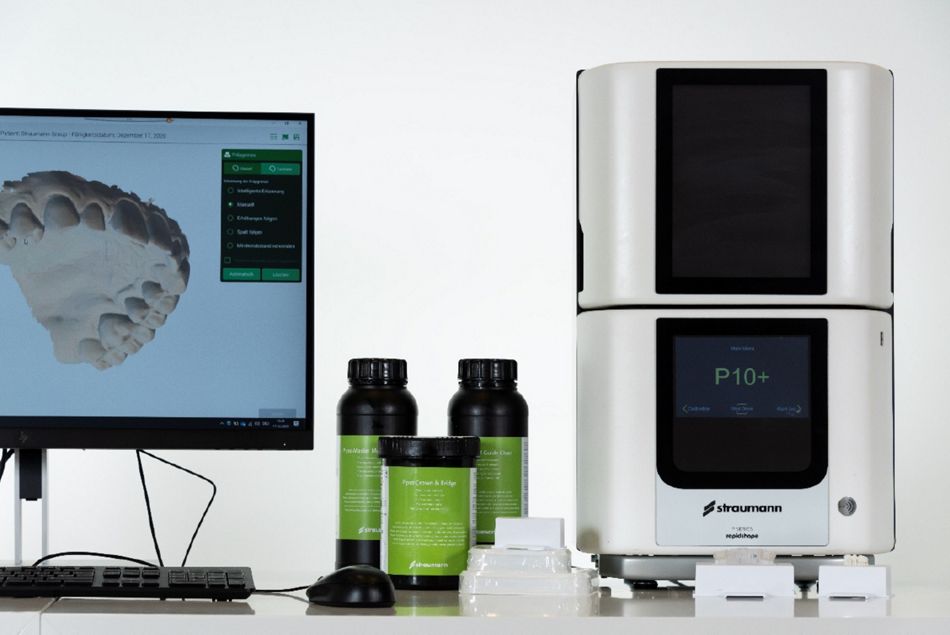
3D printing, also known as additive manufacturing, has been an ally among dental practices worldwide. Over the past decade, there have been more and more examples of clinics implementing this technology to create surgical tools, aligners, dentures, and aid implantology, reducing the need for outsourcing. This disruption has also proven to be a method of education for dental practitioners and patients through in-house digitized processes. Recognising the benefits of 3D printing in dentistry, Professor Lior Shapira, President of the European Federation of Periodontology (EFP), stated: “The digital approach is more accurate, shortens the surgical procedure, and has fewer adverse effects.”
Streamlining customised production
No one set of teeth is alike. Considering this, dental prostheses must be produced with customisation as a priority. Conventionally, this is done through CAD/CAM milling technology. As a form of subtractive manufacturing, milling can result in material wastage and calls for further manual crafting from technicians. Moreover, prostheses made through traditional methods have limitations when complex anatomy is involved. There are also restrictions regarding the volume at which crowns, implants, dentures, and other dental devices can be manufactured.
With 3D printing technologies, printed crowns and alike can be produced in various volumes in-house to avoid outside interference.
Even though dental prostheses are explicitly designed for one patient, having multiple at a dentist’s disposal would be an asset. There have been cases where the integrity of a crown has been compromised due to storage conditions and temperature changes during their transportation from a clinic to a laboratory. This leads to the crown being unfit for its intended patient. As a result, the overall restoration process will be prolonged as dental professionals have to spend time creating a new model or doing all they can to salvage the initial prosthetic. With 3D printing technologies such as Selective Laser Sintering (SLS), Stereolithography (SLA), and Digital Light Processing (DLP), 3D printed crowns and alike can be produced in various volumes in-house to avoid outside interference. This allows more room for error as technicians won't be starting from scratch when making the necessary adjustments.
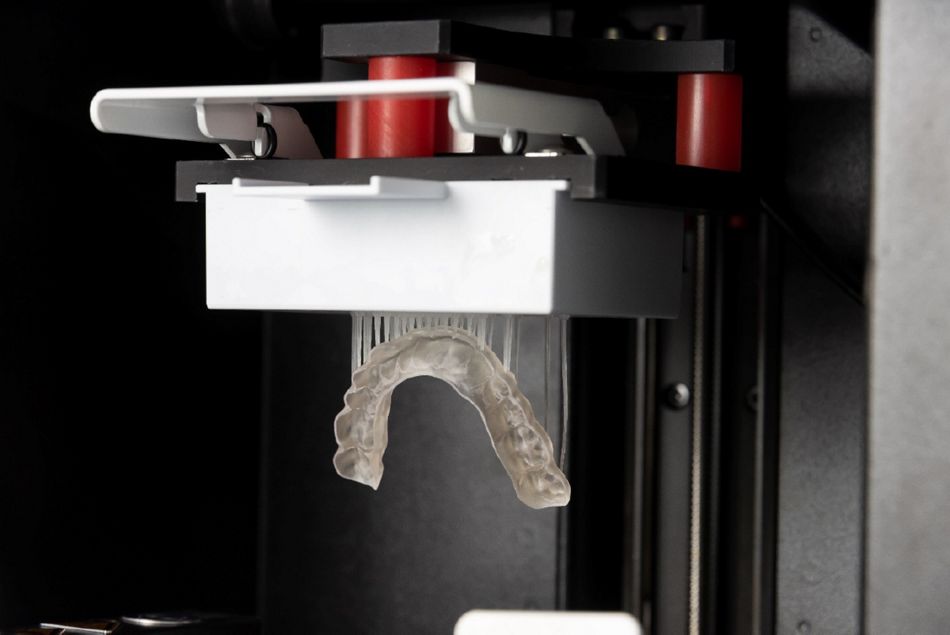